We were contracted to perform a Major Inspection on a Frame 5 Combustion Turbine for an Independent Power Producer in the Northern U.S. Upon arrival the unit was shut down and locked out to prepare for the upcoming inspection. The necessary roof sections and inlets were removed for crane access to remove components. All combustion hardware was removed during the inspection – liners, cross fire tubes, and transition pieces.
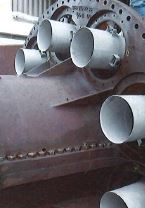
During disassembly there was a great deal of broken bolting experienced on this unit, mainly due to the fact it is an outdoor unit that has not been disassembled in many years. These broken bolts were removed by a local vendor as well as the repair of the threaded holes. The combustion hardware was not in great condition, with cracked liners and high wear on the fuel nozzles. The crossfire tubes were severely worn. Exhaust cooling air piping was also found to be severally corroded. The inlet access door was removed for inspection of the inlet and the IGV’s. The IGV angles and clearances were checked and verified. The row #1 compressor blade tip clearances were also checked. The IGV’s were cleaned for inspection. After the inspection the IGV’s with excessive clearance had the bushings replaced. The inlet was cleaned and visually inspected by our Technical Field Advisor and plant personnel prior to closing. The main oil pump was disassembled and inspected; bearings were scored so they were replaced with new ones from the customer. The spline shaft had moderate wear on the gear teeth, and was replaced as well.
The 9th stage hook fit was cracked and corroded which necessitated the removal of the aft compressor case. This section of the compressor case was removed and sent to a repair shop. Upon return to the site the aft compressor case was reinstalled with all bolting torqued to support the lower half.
All refurbished and new hardware from the customer’s inventory was checked, with serial numbers recorded and marked for location.
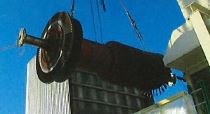
During the inspection all the upper half cases were removed as well as the upper half nozzles – 1st and 2nd. The upper half bearings were disassembled, and the rotor was removed. The number 2 bearing was found to be severally worn and out of tolerance. This allowed the rotor to drop and rub components in the lower half of the turbine section. All of the used lower half parts were removed and new or refurbished parts were installed. The rotor was cleaned, refurbished stage 1 buckets were installed, and the journals were lapped, then installed with refurbished bearings. The customer supplied new or refurbished stage 1 and 2 nozzles which were installed during the outage. All of the upper half cases were installed; all bolts were torqued per specification.
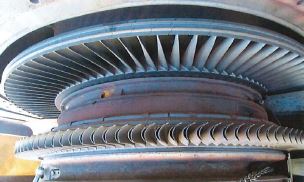
After completion of the unit the LOTO was released and the customer prepared for the test run. We were released from site after the unit was at 5MW’s and had excellent bearing vibrations.
Another great project by our Operations team, and another satisfied customer!
Wind Turbine Machining
/in News, Turbine Tips /by Mike.LakeWe recently completed another uptower wind turbine shaft machining project. Our equipment and personnel will travel to wherever the problem may be. For the wind industry, it happens to be 200+ feet above the ground, but we’re happy to do this on your turbine deck or any other area in the plant as well. Please give us a call if you have any emergent shaft machining needs, we’ll respond quickly and get your equipment back up and running. For more information on our wind turbine specialty machining services please CLICK HERE.
Before
After
3D Component Scanning
/in News, Steam Turbine Tips /by Mike.LakeIt’s that time of year again! When turbines are running throughout the summer season it’s a good time to scan any common parts that you may need to order again in the future. With our portable metrology-grade 3D scanning equipment, we are able to scan components within extreme accuracy. You can ship your components to our shop, or we can bring the experienced technicians and scanning equipment to your facility and analyze the components right there at your site. If you have any component engineering needs please give us a call. We’d love the opportunity to help in any way we can. CLICK HERE for our phone and email contact information.
Frame 5 Major Inspection
/in Combustion Turbine Tips, News, Turbine Tips /by Mike.LakeWe were contracted to perform a Major Inspection on a Frame 5 Combustion Turbine for an Independent Power Producer in the Northern U.S. Upon arrival the unit was shut down and locked out to prepare for the upcoming inspection. The necessary roof sections and inlets were removed for crane access to remove components. All combustion hardware was removed during the inspection – liners, cross fire tubes, and transition pieces.
During disassembly there was a great deal of broken bolting experienced on this unit, mainly due to the fact it is an outdoor unit that has not been disassembled in many years. These broken bolts were removed by a local vendor as well as the repair of the threaded holes. The combustion hardware was not in great condition, with cracked liners and high wear on the fuel nozzles. The crossfire tubes were severely worn. Exhaust cooling air piping was also found to be severally corroded. The inlet access door was removed for inspection of the inlet and the IGV’s. The IGV angles and clearances were checked and verified. The row #1 compressor blade tip clearances were also checked. The IGV’s were cleaned for inspection. After the inspection the IGV’s with excessive clearance had the bushings replaced. The inlet was cleaned and visually inspected by our Technical Field Advisor and plant personnel prior to closing. The main oil pump was disassembled and inspected; bearings were scored so they were replaced with new ones from the customer. The spline shaft had moderate wear on the gear teeth, and was replaced as well.
The 9th stage hook fit was cracked and corroded which necessitated the removal of the aft compressor case. This section of the compressor case was removed and sent to a repair shop. Upon return to the site the aft compressor case was reinstalled with all bolting torqued to support the lower half.
All refurbished and new hardware from the customer’s inventory was checked, with serial numbers recorded and marked for location.
During the inspection all the upper half cases were removed as well as the upper half nozzles – 1st and 2nd. The upper half bearings were disassembled, and the rotor was removed. The number 2 bearing was found to be severally worn and out of tolerance. This allowed the rotor to drop and rub components in the lower half of the turbine section. All of the used lower half parts were removed and new or refurbished parts were installed. The rotor was cleaned, refurbished stage 1 buckets were installed, and the journals were lapped, then installed with refurbished bearings. The customer supplied new or refurbished stage 1 and 2 nozzles which were installed during the outage. All of the upper half cases were installed; all bolts were torqued per specification.
After completion of the unit the LOTO was released and the customer prepared for the test run. We were released from site after the unit was at 5MW’s and had excellent bearing vibrations.
Another great project by our Operations team, and another satisfied customer!
Collector Ring Re-grooving
/in Generator Tips, News /by Mike.LakeWe were recently hired to machine and re-groove a set of collector rings on a 7FH2 Generator. This is a common service we perform during outage seasons when turbine generator outages are taking place and customers inspect the current condition of their collector rings and check groove depth. When it is noted that the collector rings need machining and/or re-grooving we are contacted to bring in specialty equipment and experienced personnel to perform these repairs on-site. The collector ring grooves and surfaces are machined, bringing the component back to within acceptable specifications. If you are ever in need of collector ring machining and/or re-grooving please give us a call. We’ll tool up and mobilize immediately and ensure we provide you with a safe, quality, efficient performance. For more information regarding our generator collector ring repairs, see our line card HERE.
As Found
Re-grooved
After Machining
Paper Mill Reopening
/in News, Videos /by Mike.LakeJust over a year ago the Phoenix Paper Mill in Wickliffe, Kentucky made their first roll of bleached hardwood pulp since their re-opening in 2019. We are proud to have helped the mill get their turbines back in operating condition, and thankful for the opportunity to be of service. The mill is vital to the Wickliffe community and provided over 200 jobs after the reopening. Now that we just passed the one-year anniversary of their initial production run, it’s amazing to look back on the work we put in, as well as the work every other employee and contractor put in during that time. Congratulations on the one year anniversary Phoenix Paper!
Summer Maintenance Checklist
/in News, Turbine Tips /by Mike.LakeSummertime is almost here! That means summer run season is beginning and many turbine generator sets will be in operation over these next few months. While the units are in operation that provides facilities with the opportunity check some items off of the to-do list. We offer a variety of non-turbine outage services during the summer months. Please see our common summer services below and let us know if there is anything we can help you accomplish.
Contact us HERE to request a quotation.
COMMON SERVICES OFFERED:
Frame 7B Combustion Inspection
/in Combustion Turbine Tips, News, Turbine Tips /by Mike.LakePSG mobilized a Technical Field Advisor, Foreman, Turbine Mechanics, and Tooling to a Utility site in the southern U.S. to perform a combustion inspection ‘’CI’’ on a GE MS-7000B combustion turbine.
The job consisted of removing and replacing all combustion parts and associated consumables. The fuel nozzles, combustion liners and transition pieces were removed and replaced with OEM refurbished components.
The bullhorns, combustion chambers, crossfire tubes, retainer clips and lid covers were returned to service with no replacement necessary. Transition piece hardware was replaced with new parts and the crossfire tubes and retainer clips were returned to service with minor wear being noted. All associated flange gaskets were replaced with new OEM consumable parts in all 10 combustion cans as a preventive maintenance practice. New flange bolting hardware was also installed as a preventive maintenance practice.
The combustion wrapper was removed to better access the transition pieces and have a better visual inspection of the 1st stage nozzle, all wrapper case bolting was replaced with new upgraded components.
The inlet was visually inspected and found to be in overall good visual condition.
A visual inspection of the exhaust plenum showed the assembly to be in overall good visual condition with minor wear noted.
The end result was another successful combustion inspection on a Frame 7B combustion turbine, and most importantly, a satisfied customer.
Over 1000 Days Lost-Time Injury Free!
/in News, Safety Tips /by Mike.LakeEarlier this month we surpassed 1000 Days without a lost-time injury. That is an amazing accomplishment by our project teams, who work in unfamiliar locations as they travel from job to job. The attention to detail and focus on safety must be at the forefront each and every day in order to avoid accidents. Keeping our teams safe has been our priority, and it shows with this accomplishment. Great job to each and every person working in the field – you make this happen!
The Right People
/in Combustion Turbine Tips, News, Steam Turbine Tips, Turbine Tips /by Mike.LakeA company built on industry leadership, knowledge and experience!
We employ industry-experienced professionals who work together consistently as a cohesive team, anticipating problems and formulating best solutions. Our team approach allows us to better organize and manage your project details and plan for contingencies. This organizational structure creates a project team that runs smoothly… So your project runs smoothly too.
Project Management
Good project management is key to a successful outage. Our Technical Field Advisors and Foremen are industry veterans, with experience across all the units we service. Many of them started their careers with an OEM. They offer the technical and project management proficiency to guide your specific project and are qualified to provide clear options and recommendations when repairs are required.
Project Coordinator
The on-site Project Coordinator manages supplies, parts, services and contractors and reports costs on a daily basis. This allows us to manage your project with a single Technical Field Advisor, reducing costs and providing seamless control.
Turbine Mechanics
Each Foreman builds a base crew of Mechanics who work together consistently. We also provide formal training and advancement for a pool of mechanics who are utilized when larger crews are needed. Together, they have the necessary skills and experience, and know our tools, procedures and safety.
Remote Turbine Consultations
/in Combustion Turbine Tips, News, Steam Turbine Tips, Turbine Tips /by Mike.LakePower Services Group offers remote consultative services for those customers looking to resolve issues on their turbine power island. Many facilities have postponed or delayed outages this year, and that may extend turbine run times to longer than some may be comfortable with. Many turbines may have had outages planned to address issues currently being experienced. Those outages are now postponed, and facilities must make alternative plans to address any operational issues. At PSG, we can provide remote assistance to help you develop solutions to any potential problems you may be facing. We will offer our opinion based on the information gathered remotely between your plant personnel and our qualified Technical Advisors. This may include any operational data or photographs related to the issue being experienced, telephone conversations between involved parties, and remote video meetings by telephone to allow our Technical Advisors personally experience any sights and sounds that may be the result of the issue you are experiencing. At PSG, we are here to help. We understand that it may not be the most optimal time to have outside personnel visiting your facility, so we will do everything possible to help you develop alternatives through our remote consultative services with our qualified Technical Advisors.
We have expertise on most Steam Turbine OEM types (List of Steam Turbine OEMs we perform services on), as well as various types of Combustion Turbines (List of Combustion Turbine OEMs we perform services on).
You can call us at any time to begin discussions at 800-226-7557, or email us through the following link: Contact Us.
If you ever experience an emergency situation, we have Technical Advisors just a phone call away at 888-MrTurbine. We are available 24/7, 365 Days a year.
We look forward to helping you ensure your turbine is operating as efficiently as possible until your next turbine inspection.