We were contracted to perform a Major Inspection on a Frame 5 Combustion Turbine for an Independent Power Producer in the Northern U.S. Upon arrival the unit was shut down and locked out to prepare for the upcoming inspection. The necessary roof sections and inlets were removed for crane access to remove components. All combustion hardware was removed during the inspection – liners, cross fire tubes, and transition pieces.
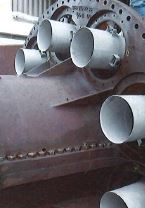
During disassembly there was a great deal of broken bolting experienced on this unit, mainly due to the fact it is an outdoor unit that has not been disassembled in many years. These broken bolts were removed by a local vendor as well as the repair of the threaded holes. The combustion hardware was not in great condition, with cracked liners and high wear on the fuel nozzles. The crossfire tubes were severely worn. Exhaust cooling air piping was also found to be severally corroded. The inlet access door was removed for inspection of the inlet and the IGV’s. The IGV angles and clearances were checked and verified. The row #1 compressor blade tip clearances were also checked. The IGV’s were cleaned for inspection. After the inspection the IGV’s with excessive clearance had the bushings replaced. The inlet was cleaned and visually inspected by our Technical Field Advisor and plant personnel prior to closing. The main oil pump was disassembled and inspected; bearings were scored so they were replaced with new ones from the customer. The spline shaft had moderate wear on the gear teeth, and was replaced as well.
The 9th stage hook fit was cracked and corroded which necessitated the removal of the aft compressor case. This section of the compressor case was removed and sent to a repair shop. Upon return to the site the aft compressor case was reinstalled with all bolting torqued to support the lower half.
All refurbished and new hardware from the customer’s inventory was checked, with serial numbers recorded and marked for location.
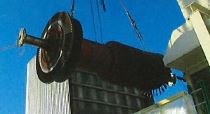
During the inspection all the upper half cases were removed as well as the upper half nozzles – 1st and 2nd. The upper half bearings were disassembled, and the rotor was removed. The number 2 bearing was found to be severally worn and out of tolerance. This allowed the rotor to drop and rub components in the lower half of the turbine section. All of the used lower half parts were removed and new or refurbished parts were installed. The rotor was cleaned, refurbished stage 1 buckets were installed, and the journals were lapped, then installed with refurbished bearings. The customer supplied new or refurbished stage 1 and 2 nozzles which were installed during the outage. All of the upper half cases were installed; all bolts were torqued per specification.
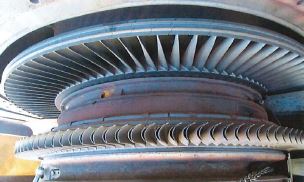
After completion of the unit the LOTO was released and the customer prepared for the test run. We were released from site after the unit was at 5MW’s and had excellent bearing vibrations.
Another great project by our Operations team, and another satisfied customer!