Pre-Outage Planning
A Customized Plan
Most power producers are short-staffed and do not have the time and sometimes the expertise to prepare a comprehensive outage plan and workscope. That’s why we offer the option of providing our comprehensive Pre-Outage Planning Service independent of the award of the contract for inspection and repairs.
Our field project teams have the breadth of knowledge and experience to produce the highest quality planning product, with a workscope customized to your unit and its specific signature.
One of our qualified Technical Directors will visit your plant and prepare a customized report for your specific unit. The report will contain everything needed to plan your internal preparations for the outage and to prepare a comprehensive Request for Quote for the inspections and repairs.
A Basis For Your RFQ’s
Your customized Pre-Outage Plan will include everything you need to prepare a comprehensive Request for Quote for the necessary inspections and repairs. We will compile a summary of the findings from past inspections and develop a list of recommendations for potential repair work. We will prepare a comprehensive and detailed suggested Statement of Work for the outage, based on these findings and observations from a unit walk-down. Incorporating this information into your Request for Quote packages will yield “apples to apples” cost comparisons and few if any surprises on implementation.
A Task List For Your Facility
We will review your spare parts inventory and compile a list of recommended parts to have on hand prior to the outage. We will recommend disposal of any expired or unusable spare parts.
We will also prepare a Critical Path Method schedule based on the defined workscope. You can use this schedule to plan your expected outage duration and coordinate with any other activities to be conducted during this downtime.
What We Provide
The Pre-Outage Planning Package includes:
- Outage History Review: We review your past outage reports to determine pending or implemented outage recommendations and any changes that may have been made to your unit.
- Unit Walk-down: We perform a detailed walk-down of the unit, visually inspecting the components and auxiliaries that will help to develop a detailed pre-outage scope of work.
- Customized Outage Workscope: Formulated from the on-site analysis of your unit, past outage reports, and known issues supplemented by discussion of particulars with you and your staff, we develop a workscope unique to the specifics of your unit and its current condition.
- Outage Schedule: We take your customized workscope and create a comprehensive Critical Path Method schedule. This exceptional tool outlines a reasonable outage schedule and projected duration, and it can be used as a guide to measure the performance of your outage contractor.
- Parts List: We compile a “recommended to buy” list determined by a physical review of your unit, prior outage report recommendations, and review of available inventory.
In summary, our Pre-Outage Planning deliverables to you will be:
- A scope of work tailored to your equipment and outage needs.
- A parts inventory and suggested purchase list (to support outage or emergency needs).
- A document to assist in the preparation of the scope for RFQ / bid documents.
Please CONTACT US today to learn more about how we can help you plan your next turbine outage.
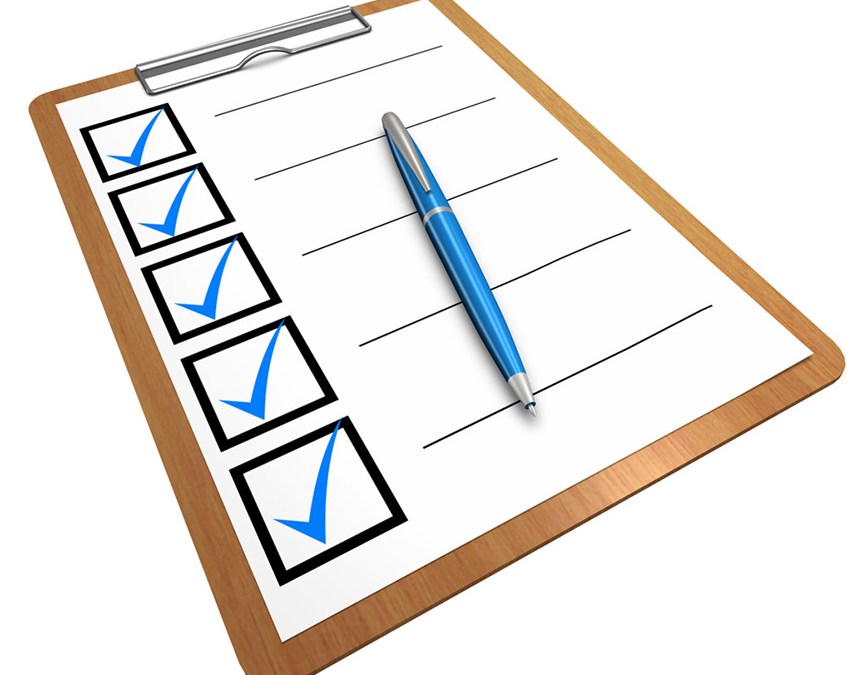